Overview
Variable compactability control auto-adjust set point
IIoT Based Compactability Control Solution For Improved Casting Outcomes
One of the critical control levers for good casting outcomes is the control of moisture. Moisture being directly proportional to Compactability, the control of the Compactability assumes significant importance in the sand preparation process.
The key to good Compactability control is the set-point at the mixer which determines the Discharge Compactability (DiCo) and ultimately, the Lab Compactability (LaCo). Therefore, the importance of determining the most optimal set-point at the Controller cannot be overstated.
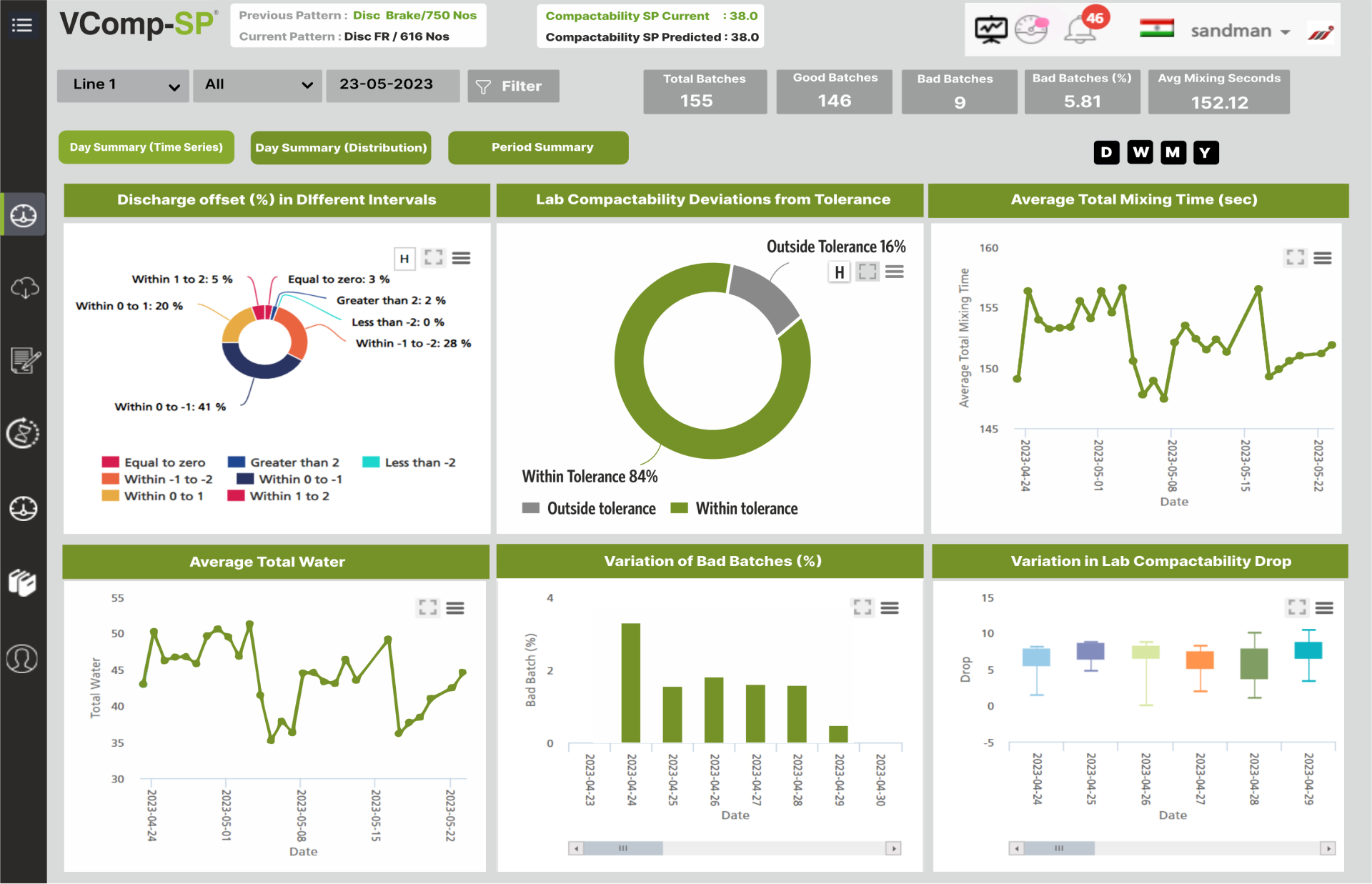
In the absence of adequate data support of factors influencing Compactability such as ambient humidity, temperatures, return sand moisture and many more; the Compactability setpoint (CoSP) is determined experientially by the process owner and is changed from time to time also based on experience. Often, the time intervals of varying the set-points are laggard to the ever-dynamic conditions of the sand loop. This results in a variance in lab Compactability. If the LaCo variance is significant, this may lead to related sand rejections like sand inclusions, swelling, shrinkage and sand fusion due to varying mould integrity and quality.
MPM INFOSOFT has developed a unique Variable Compactability Control Software: "VComp-SP®" , leveraging both current and real-time data from SCADA and sensors, to enable foundries to dynamically predict and variably adjust set-points at the Mixer/ Controller.
VComp-SP® is an enhancement and an addition to the compactability controller function and is not it's substitute.
MPM INFOSOFT can design, install and digitize the complete loop of the sensors and interface with available SCADA . The data so captured will become a significant source of valuable insight into and proactive control of one of the most crucial ratios of a foundry sand system: Compactability to Moisture ratio.
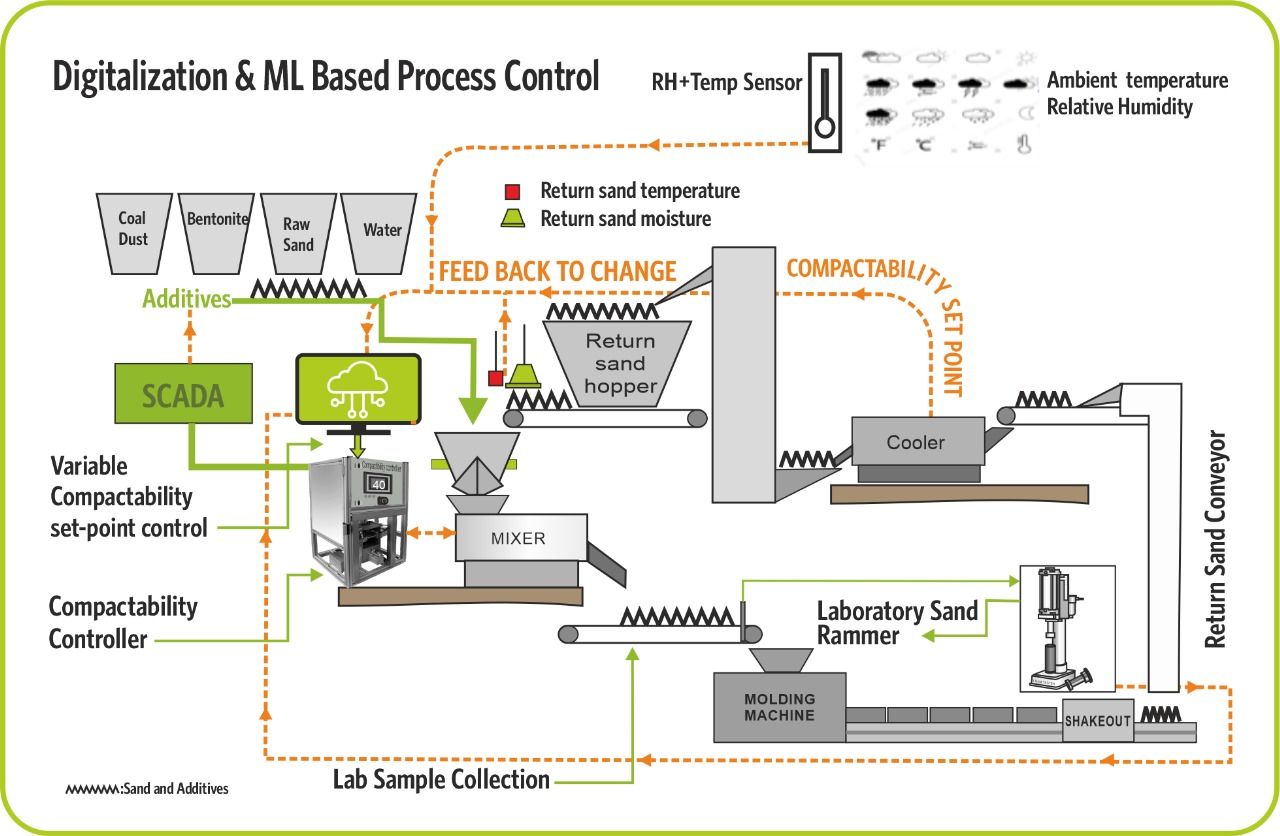
Salient Benefits:
The Compactability set-point is predicted at rule-based time intervals.
The Prediction of a set-point is based on real-time or measured data.
Reduces the variability in Lab Compactability (LaCo).
Improves mould quality and reliability.
Keeps the Lab Compactability close to Optimal/ Target compactability.
Reduces incidence of mould quality related rejection.
Integrates available SCADA and sensor data.
Improves Compactability to Moisture ratio.
Built-in process deviations alerts enables preventive action/maintenance.
It is possible to auto-set the CoSP (Compactability set-point).
VComp-SP® Case Study
GOALS:
To dynamically predict compactability set point using IIoT-based data analytics approach to achieve target lab Compactability for better mould integrity & therefore, casting outcomes.
BACKGROUND:
The VComp case study was carried out at a renowned casting manufacturer in Northern India, having manufacturing capacity of 25,000 tons/annum. The bunch weight exhibited variations ranging from 15 to 34 kg, while the sand-to-metal ratio spanned from 4 to 10. Additionally, the average weight of the cores used in the casting process was measured at 0.4 kg, with a wide variation from 0 to 1.77 kg.
The foundry was facing high variability in the moisture content of the prepared sand and inconsistency in lab Compactability. These inconsistencies led to sub-optimal mould quality and related rejection rates. To address this, the foundry implemented VComp-SP® , an IIoT driven advanced data analytics software solution.
With VComp-SP®, the foundry gained near precise control over the moisture content of the prepared sand and achieved consistent lab Compactability in close tolerances. The software provided the capability to dynamically adjust the Compactability set-point based on the specific characteristics of the return sand, ambient conditions, and casting requirements. By leveraging the power of IIoT and data analytics, the foundry optimized the Compactability set-point to minimize variations and ensure optimal casting performance.
The successful implementation of Sandman VComp-SP® resulted in improved rejection rates and enhanced operational efficiency for the foundry. The precise control over moisture and Compactability, combined with the variable set-point prescription, significantly reduced casting defects and enhanced overall quality.
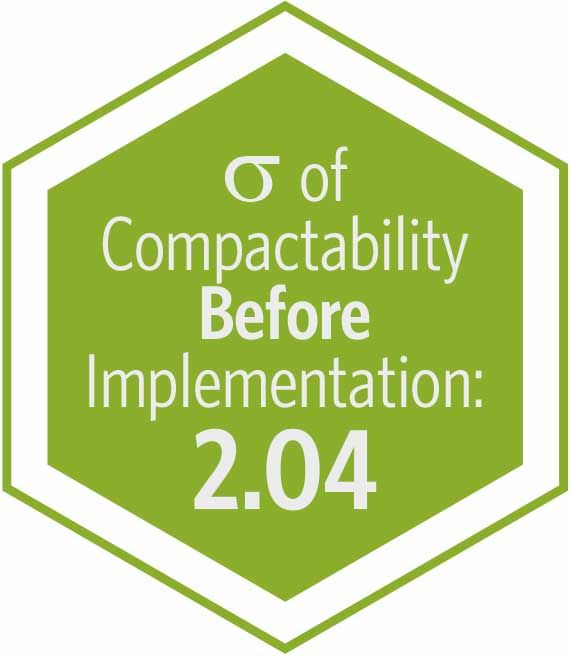
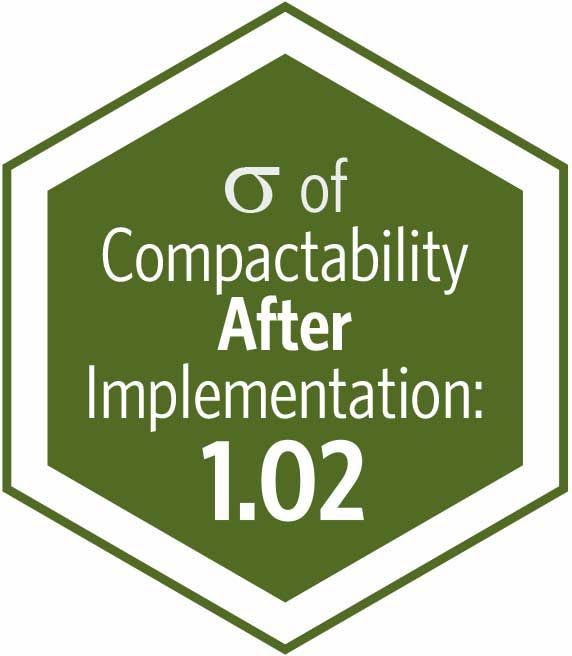
IMPORTANCE OF COMPACTABILITY CONTROL
Critical control lever of Moisture
Control of mould dilation
Vital indicator of mould integrity
CHALLENGES
Estimation of drop from Compactability to mould
Experiential set-point by Process Manager
Dynamic ambient, sand conditions impact drop
Constant set-point irrespective of jobs/castings.
SOLUTION
Analytically driven decision support correlating environmental and return sand factors to achieve desire lab Compactability (optimum) via dynamically variable Compactability set-point
BENEFITS
The Compactability set-point is dynamically variable.
The Prediction of Compactability set-point is based on the real-time or recent data.
Keeps the lab Compactability close to Optimal Compactability.
Reduces incidence of sand related rejection like shrinkage, fusion and mould dilation.
It is possible to auto-set the CoSP.
Reduction In Standard Deviation:
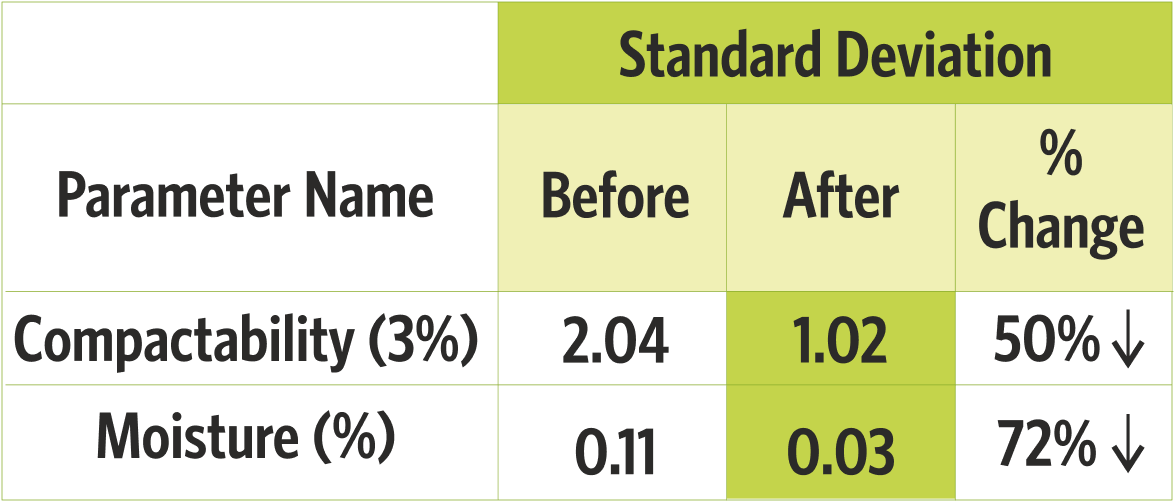
Standard deviation is reduced for Compactability and Moisture by more than 50% after implementation where is running, compared to the period before implementation.
The key to good Compactability control is the set-point at the mixer which determines the Discharge Compactability (DiCo) and ultimately, the Lab Compactability (LaCo). Therefore, the importance of determining the most optimal set-point at the Controller cannot be overstated.
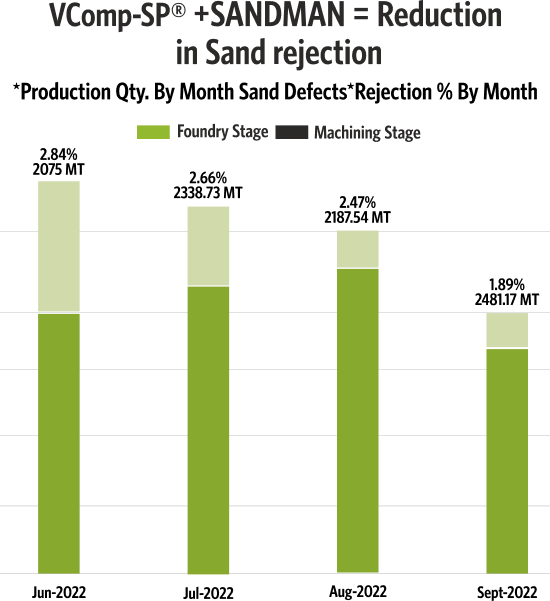
By using both VComp-SP® and SANDMAN® in tandem to control the sand parameters it has been observed that there has been a reduction in total sand rejection from 2.84% to 1.89%.
The implementation of VComp-SP® has shown a clear and evident sensitivity of the lab Compactability to variation of the Compactability set-point at the mixer/controller based on input variables.
The reduction in the sand related rejection demonstrates that Compactability control has a clear impact on related sand rejection and therefore deserves increased importance in green sand foundries.