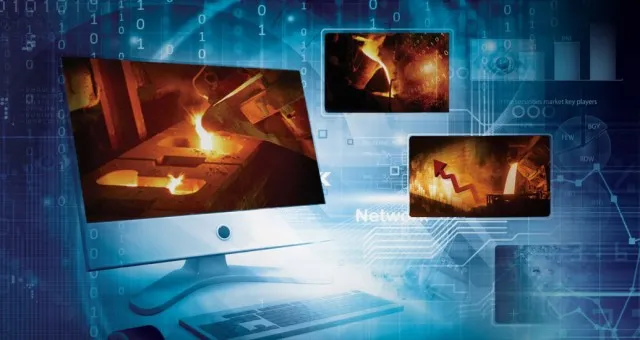
SANDMAN - The world's first data analytic driven solution to reduction in casting rejections by process optimisation
SANDMAN is about
Metal Castings is one of mankind's first innovation in graduating from tools made of bone, wood and stone, to cutting, mining tools and hunting tools and weapons made from metal.
Over the Eons, metal casting industry has developed into a very precise science and pervades almost every aspect of Mankind's industrial endeavour whether in the realm of motion, automation, space or just everyday life.
Foundries are the producers of castings. One segment of metal castings in foundries is Iron cast in green sand moulds.
Relying on sand, water, natural clay (bentonite) and carbonaceous addi- tives; to make moulding sand and converting this mix into a 'mould' , foundries process ferrous scrap, pig iron, ferro alloys into a Cast shape of Iron.
Along the way, The casting process also generates “casting rejections”. Casting rejections are those components which have defects like blow- holes, sand fusion, scabs, etc. While the component itself can be recy- cled by recharging into the furnace for remelting, its rejuvenation into a new component requires the following:
- Additional electrical energy (0.700 MW) per ton of scrap.
- Fresh additions of inoculants and alloys.
- Fresh requirements of new sand, clay and additives
- Additional labor, electricity, productive capacity.
The real impact of casting rejection is however the following:
- Generation of toxic waste along with disposal of 'used' sand
- Generation of CO2 emissions due to use of electrical energy to not only remelt the scrapped casting, but also associated with the re- process.
- Carbon footprints.
- Waste of natural resources like sand, water, clay and carbonaceous additives.
MPM Infosoft is a pioneer in the design and development of cutting edge data analytics software, analytical tools and services for reducing wastage thereby improving productivity and improving environmental performance in the field of castings related to moulding sand practice.
SANDMAN® conceived and invented by Mr. Deepak Chowdhary, a do- main expert in this field; and developed and marketed by MPM Infosoft is the direct result of this endeavor.
Why SANDMAN®?
Green sand control and it's importance in modern day foundries costs.
In these times of fast changing economic scenarios, business eco sys- tems & the resultant increasing pressure on business sustainability, castings rejections and their control in green sand foundries assume a huge dimension of cost and potential saving of repetitive lost profits.
The Problem & the Un-Met Need of Foundries Globally
Times have changed and there is an increasing gap between experi- ence and skilled manpower to manage the green sand molding process which has always been known as an 'art'. The element of the human interface in this process management is becoming increasing limited as the process grows faster, more exact and increasingly dependent on fast depleting, standardization resistant, natural resources like silica sand and bentonite.
As people age, change, move on, the legacy of the experience and knowledge of the foundry sand process and management is often lost or available only in limited spots to the succeeding controllers.
Foundry sand and related rejection Data is often recorded in non stan- dard formats making data retrieval and even basic analytical capabili- ties, difficult and most of the times questionable for accuracy, integrity and veracity of the data.
Most foundry data is often just a collection of thousands and millions of points which beg to be made meaningful as they are the treasure trove of the foundry for profit if processed by modern data science and modelling methods.
As the data points become huge, even the most experienced sand manager cannot be expected to keep an all encompassing perspective of precise experience over a huge process-variable scenario.
Validation of most foundry processes is almost always at the cost of the foundry. Serious costs can occur because the effects are felt in the long term. Course Correction logic is often mired in reactive decision making and limited experience of human interface.
It hurts the foundry, immensely.
There is therefore a huge un-met need for a discerning foundryman to use modern data science techniques based on mathematical modelling and algorithms to mine his/her own historical and experiential data to convert repetitive loss of profits due to rejections into reclaimed profits.
The Solution
SANDMAN® is a unique world-class software service conceived, created and developed by Mr. Deepak Chowdhary, founder owner of MPM Private Limited which, for the first time in the world, offers a data analytic driven, software solution which enables foundries to gather, organise, validate & store reams of data and use advanced and powerful mathematical modelling to interpolate, analyze and process this huge data over time periods which are limited only by their own capacity to enter their data.
In doing so, the power of multi-parameter analytics enables the foundry to detect and analyse the most influential (deviant and/or aberrant) process parameters of the green sand, over any specified time period within the own data of the foundry. It gives the power of predictive analysis on the various rejection incidences vis-a-vis the most influencing green sand parameters at any point of time in the foundry's historical data set and model.
This allows the foundry to take timely corrective actions to bring about process consistency and most importantly, move from reactive to for- ward looking, predictive green sand control.
This SaaS, web based service which does not require any capex in hardware, is available through unique ID and Password which enables the Foundry to access their sand related information 24/7 from their own location without any time lag.
The salient features of SANDMAN® are descriptively detailed in the attached Brochure. However, besides the features there are several col- lateral advantages when SANDMAN® is deployed in a foundry:
- Installation of Data Discipline through the rank and file of the mold- ing sand preparation process owners.
- Ensuring data integrity, veracity due to the powerful Data Validation feature which restricts the loading of aberrant/inaccurate data.
- Installing a process and sense of data ownership in the organisation when process control brings about reduction in rejections and re- claimed lost profits.
- The Historical and Experiential data, recorded through the unique annotation feature, ensures that the foundry is the owner of this data legacy without limitation in its lifetime.
- reduces the reliance on changing human interface and ensures transfer of experience accurately and comprehensively to succeeding managers so that costly mistakes are not repeated and right decisions are not overlooked.
- The Powerful Data Analytics enable the foundry to identify in a couple of clicks which parameters in the molding sand are impacting rejections the most on any given day. This enables the user to move from reactive decision making to forward looking and more accurate course correction decisions.
- Reduces reliance on dwindling domain experienced human interface
- There is no product/brand/extraneous Bias in the decision making.
- Reduction in rejections, besides improving productivity by default, save or reduce:
- cash and revenue loss
- costly additives like sand, lustrous carbon formers, bentonite and water.
- Environmental impact:
- electrical energy
- toxic sand waste generation and disposal issues.
- carbon footprints
- The Powerful, yet user friendly SPC tools, enable validation of the decision making and bring about a measurability of the performance metrics.
- SANDMAN® enables senior managers and high ranking management total overview of the foundry's state of the system sand and rejec- tions, causes and solutions in a few clicks.
However, no brochure can describe the true power and scope of SANDMAN® which can be best experienced in actual deployment in foundry operational conditions.